编辑推荐: |
本文主要介绍了自动驾驶的必要条件--线控底盘相关知识。希望对你的学习有帮助。
本文来自于微信公众号攻城狮杨工,由火龙果软件Linda编辑,推荐。 |
|
0 序言
自动驾驶的五个系统,感知、定位、决策、规划和执行。其中执行系统的讨论度最低,但其实自动驾驶对于执行系统也有一定的要求,需要其在原有的技术上进行迭代升级。执行系统通常是指车的底盘,实现驱动、制动、转向和减震等功能。传统的汽车底盘如下图所示。
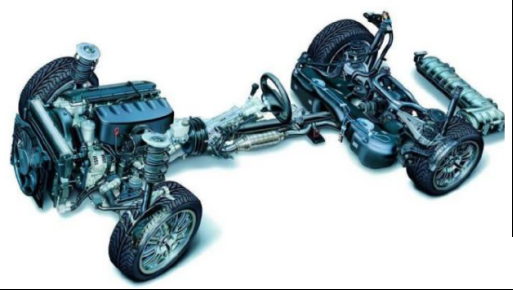
人开车时,如果想减速,需要脚踩刹车踏板。刹车踏板接受人脚施加的力,车的机械系统会将该力进行放大,这个力最终会传导到车的刹车片上,使得车轮停止转动。说到自动驾驶,没有人的介入,就无法踩刹车踏板。所以,对于自动驾驶而言,其底盘不能依靠外力输入-放大-执行这样的系统。自动驾驶系统的硬件部分是电气化的,在这个系统中,交互的是电信号,所以自动驾驶所需的底盘系统一定是可以电控的。
在原先的机械式的底盘系统上加电气化的输入接口,不谈性能,只谈功能的话,其实就可以勉强满足自动驾驶的需求。比如原先需要人的外力驱动的,那么我们在输入端改成一个电机。我们给电机一个信号,让其模拟人给的驱动力。但其实我们还想尽量减少底盘系统中机械结构的占比,将传统的机械、液压或气动等连接模式转换为导线。还是以刹车为例,二者的区别如下图所示。
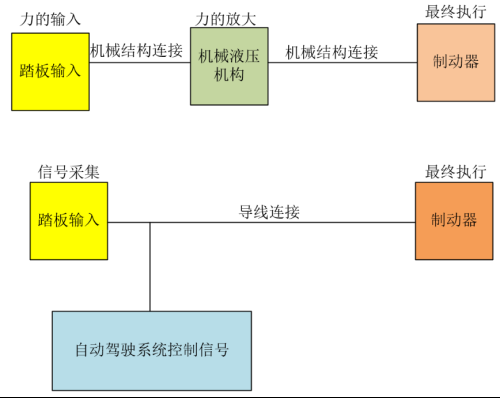
这种将驾驶员的操纵动作通过传感器转变为电信号或者自动驾驶系统直接给电信号,然后通过电缆传输到执行机构的技术,我们称之为线控技术(Drive-by-wire)。线控底盘如下图所示,相比传统的底盘要精简很多。
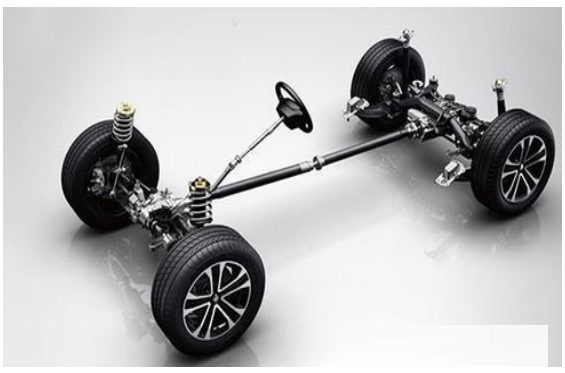
推广线控底盘主要原因有以下几个。
(1)自动驾驶要求实现人机解耦:这就是上文说的,自动驾驶系统需要在没有人介入的情况下操作底盘系统。以刹车为例,刹车踏板相对于一个操作界面,刹车踏板与车轮上的制动器并没有直接的机械连接,刹车踏板只相当于一个操作单元。当人踩下去后,根据踩下的行程,系统会得到一个对应的制动力信号,系统会将这个信号通过导线告知车轮上的制动器并让其动作,这里的制动器就是执行单元。既然执行单元的输入是一个电信号,那么人的动作就不是必须的。当处于自动驾驶状态时,系统就可以根据决策判断给出对应的电信号。这就实现了人和制动器的解耦。
(2)线控具有精度高、响应快、安全性高等特点:随着自动驾驶技术的发展,自驾等级不断提高,也对执行机构的响应速度和控制精度要求越来越高。电信号相对于机械液压,其信号传输和响应速度更快,控制也更加精准。同时,执行单元使用外来能源执行操作命令,其执行过程和结果受电子控制器的监测和控制,也有利于在遇到紧急工况时保证驾驶员和乘客的安全,因此线控底盘亦具有高安全性的特点。
(3)电子电气架构升级需要线控技术:分布式架构下,制动、转向、驱动为独立子系统,由单独的ECU分别控制,由于底盘运动执行信号来自驾驶员,各子系统协同需求较低。随着整车智能化程度的提升,分布式架构存在各子系统难协同、网络结构复杂、软硬件耦合关系强、无法统一OTA升级等问题。因此,中央域控的电子电气架构成为趋势,在这种架构下,需要实现底盘运动控制的集成化和协同化,线控底盘技术可以满足这一需求。关于电子电气架构的内容,可以查看我之前的文章。
电动汽车EEA架构
(4)线控技术有助于减轻底盘的重量,节省车内空间,对电动车续航和汽车环保有重要意义:导线重量整体低于机械、液压等传统零部件,推广后有益于减轻车身重量,提升电动车续航。在高阶自动驾驶中,制动转向等关键环节需要实现冗余设计,考虑到车内空间、信号传导机制、响应精度等因素,以线控来替代机械结构也是必然的。
同时,导线布局较为灵活,对于平衡车辆重量具有显著帮助,这对于提高车辆行驶稳定度和体验感、提高续航里程和燃油经济性等具有重要意义。此外,线控底盘去除了制动液等对环境具有污染性的物质,有助于进一步强化新能源汽车环保属性。
综上,线控技术是底盘技术升级的确定性趋势。线控底盘可以分为线控制动、线控转向、线控悬架、线控换挡、线控驱动/油门(燃油车叫线控油门,电动车不烧油,叫线控驱动),本文先介绍线控制动。
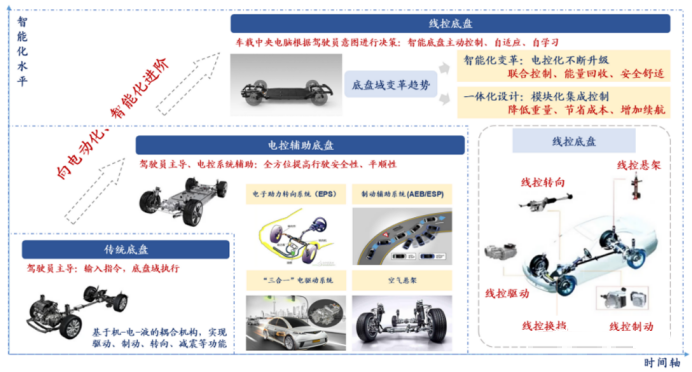
车辆制动系统分为驻车制动与行车制动。驻车制动指车辆静止时通过制动器锁住传动轴或车后轮,避免溜车;行车制动是指在车辆前进过程中,驾驶员通过操作制动踏板,给予车轮制动力,使车速降低或停车。
1 驻车制动
我们先来看传统的机械驻车制动器,如果学车学的早,大家应该都记得在停车的时候要拉个手刹(有的车是脚刹),保证车不溜车。
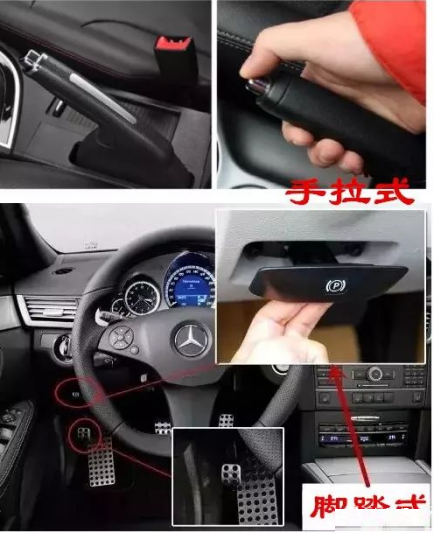
它们的学名叫做驻车制动器,这是相对行车制动器而言的,其结构如下。拉起手刹后,带动拉绳使得车轮制动器内动作。
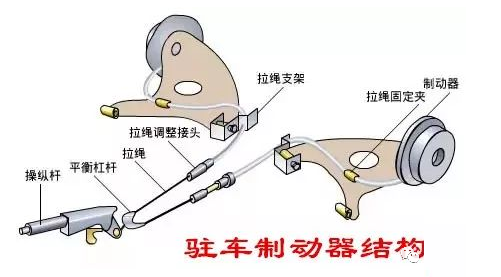
上图中的制动器是鼓式的,正常工作时,制动鼓与车轮一起转动,当拉起手刹后,力通过拉绳传递到制动轮缸,制动轮缸推动制动蹄向外扩张与制动鼓的内壁接触,产生摩擦力,使得车轮刹停。
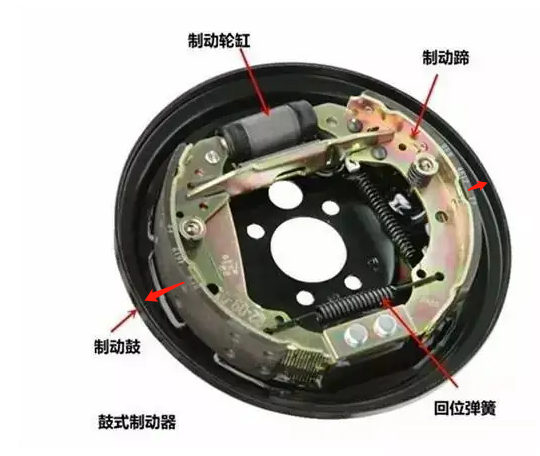
想象一下,你把一只手放到一个玻璃杯内,用另一只手转动玻璃杯。如果玻璃杯内的手不用力,则玻璃杯可以顺畅转动。当杯内的手向外撑开,则你的手和玻璃杯就产生了摩擦,玻璃杯就转不动了,这就是鼓式制动器的基本工作原理。制动器类型还有其他的,并不是说驻车制动器只能是鼓式的,只是上面的图正好是鼓式制动器,所以展开讲了一下。
与机械式刹车相对的,是电子手刹,Electrical Park Brake,即EPB。电子手刹分为两类,第一类是钢索牵引式,如下图所示。
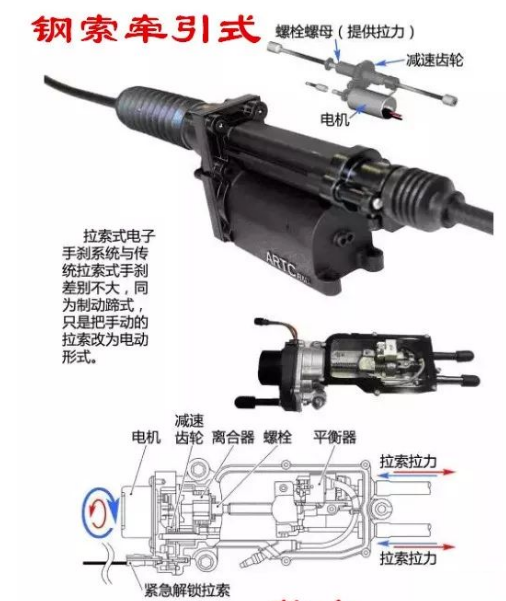
这类EPB与传统驻车制动器的区别是,不需要人工去拉手刹或者脚踩脚刹,而是通过一个按钮,给一个电子信号,电机便开始驱动去拉动拉绳。
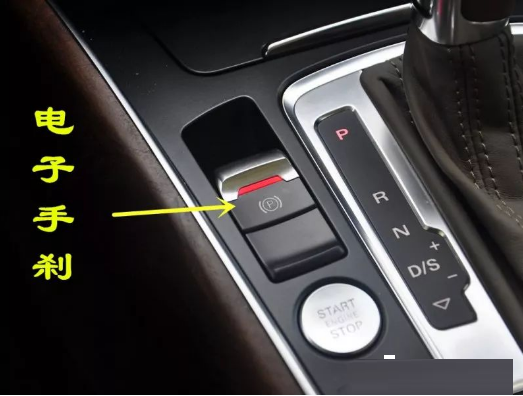
拉绳的作用是将源端的力传递到终端的制动器,那为什么还要拉绳呢?直接在终端放一个电机,把电信号送到终端的电机上,让其发力去刹车不就好了?这就是整合卡钳式电子手刹。下图中的这种制动器与前面的鼓式制动器不一样,这是盘式制动器。可以把刹车片看作是和车轮是连在一起的,刹车卡钳左右两边有制动块,需要制动时,电机推动制动块贴近刹车片,就可以使其刹停。
类似于一个车轮在滚动,你两只手从两边拍在轮胎上,用力夹紧,这就可以使其停下来了。
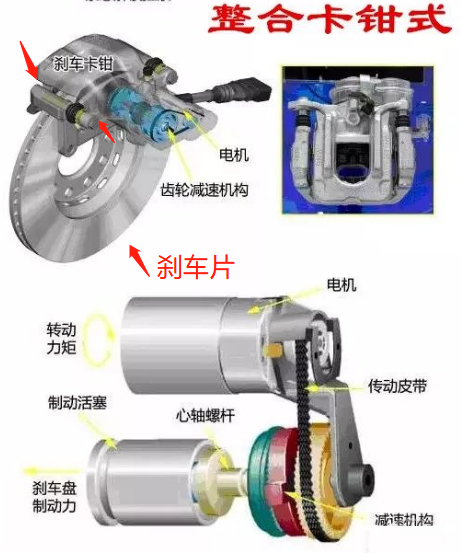
EPB在优化座舱空间布局的同时,也避免了由于手刹未拉紧或设备磨损所可能导致的制动力下降,提升驻车安全。更重要的是,电子化驻车是遥控泊车(RPA)、自主代客泊车(AVP)等功能的必要环节,也为高级别自动驾驶方案奠定基础。
传统机械制动与EPB的对比总结如下。
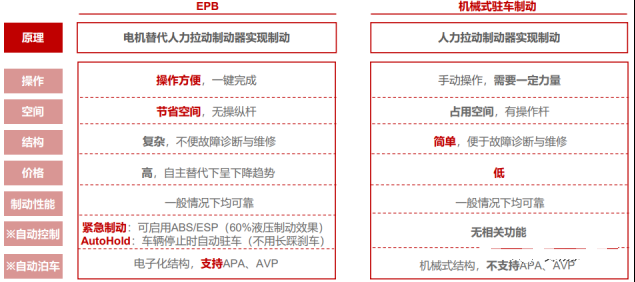
目前EPB的主要供应商如下。
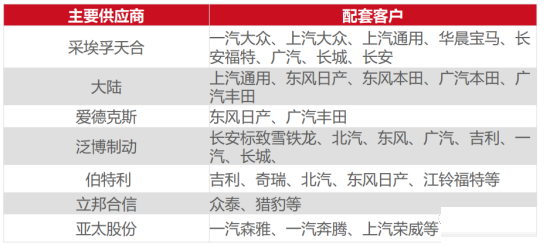
2 液压行车制动
行车制动方面,我们先看传统的行车制动方式。在此之前,要先回忆下帕斯卡定律,如下图。下图中的F指的是活塞受到的力,P指的是活塞的面积。两个活塞之间是密闭的腔体,里面是液体。由于液体的体积不可压缩,因此液体中处处受到的压强是一致的,压强=力/面积。
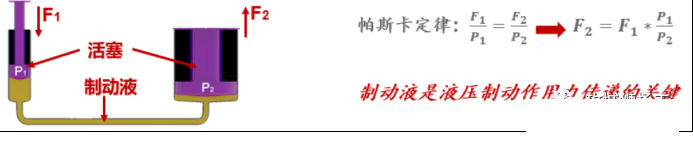
如果我们在左边施加一个F1的力,就可以在右边得到一个F2的力,F2的大小与F1还有两边的受力面积有关。
帕斯卡定律应用在汽车制动系统上的原理如下图所示,如果觉得图不够清楚,可以搜索华西证券的报告《线控底盘:智驾驱动
自主崛起》。
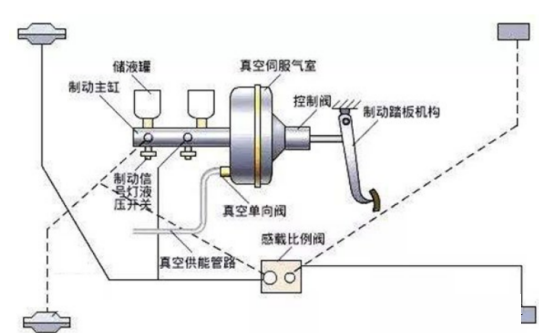
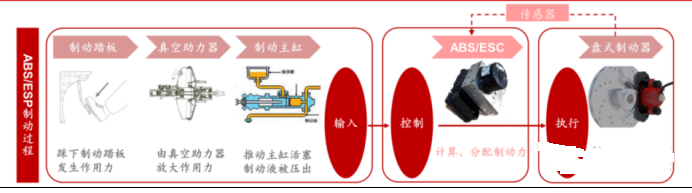
驾驶员与制动系统直接接触的就是刹车踏板了,要知道车本身的质量很大,纯靠人的蛮力去踩刹车想要刹停是很费力的,所以需要有个模块来放大我们输入的力。在液压制动中,真空助力器用来放大外力。关于真空助力器的工作原理,请看下面的视频(我觉得看视频的理解效果最佳)。微信公众号无法直接链接到原视频,也可以在B站搜索视频标题。参考视频链接
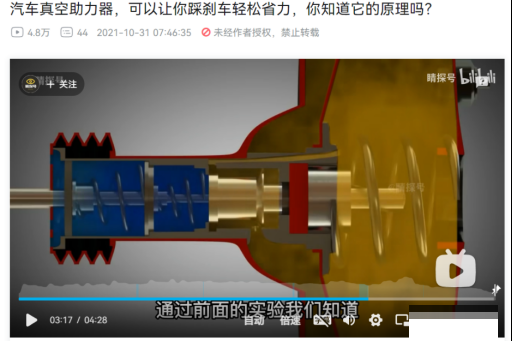
主缸上方有储油罐,主缸内部有活塞,当真空助力器带动主缸内的活塞运动时,制动液会被从主缸内压出。主缸的工作的原理请看下面的视频。参考视频链接
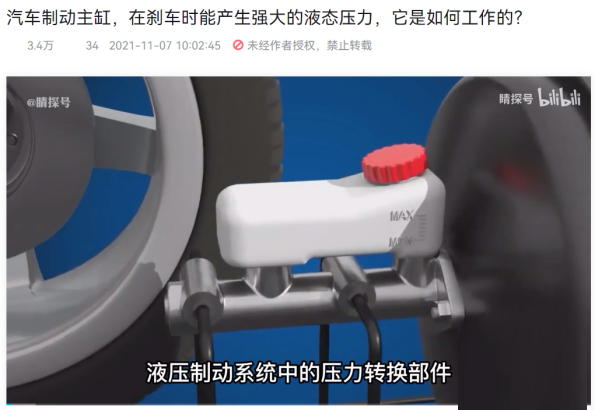
制动液被压入到最终的制动器,目前乘用车上常用的是盘式制动器。盘式制动器上的制动块夹住制动盘,最终刹停轮胎。盘式制动器的工作原理上面有简略讲过,详细的可以看下面的视频,更直观一些。参考视频链接
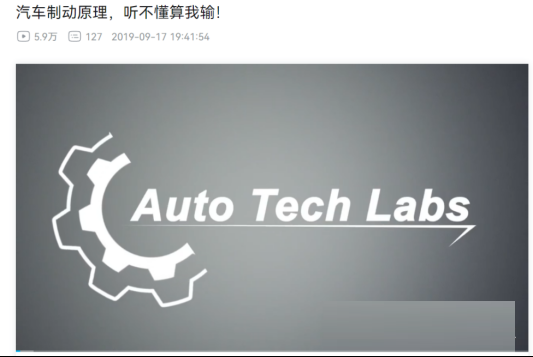
制动器具体可分为盘式制动器、鼓式制动器、盘鼓式制动器。上面我们已经看过了鼓式和盘式了,盘鼓式有点像二者的结合体。下面简单对比一下三种制动器的区别。
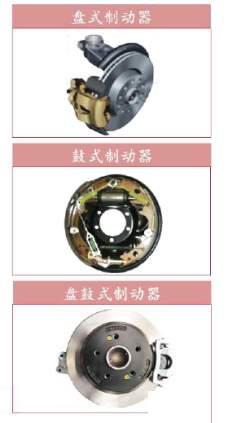
盘式制动器由于散热能力好,不容易出现热衰退,制动力比较稳定,相较热衰退明显的鼓式制动器更适用于乘用车,随着盘式制动器成本逐渐降低,乘用车制动器分布逐渐从“前盘后鼓”变为“四轮盘式”,盘式制动器逐渐成为市场主流。而盘鼓式制动器仅用于后轮,将盘式制动器与鼓式制动相结合,盘式制动器用于行车制动,鼓式制动器用于驻车制动,是“前盘后鼓”向“四轮盘式”转变的过渡期产品。如果觉得文字乏味,可以看下面是视频解解乏。参考视频链接
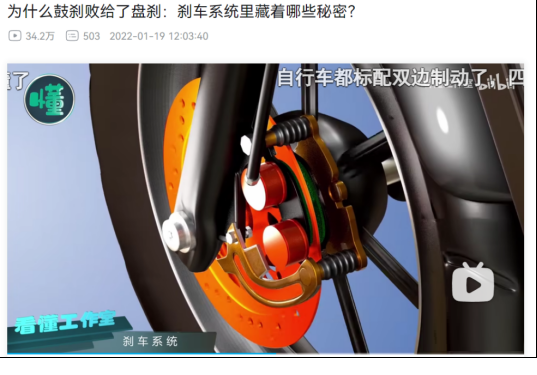
3 电子稳定控制系统
按道理下面就应该讲行车制动的演变,但在此之前要讲讲电子稳定控制系统,即下图中的ESC。
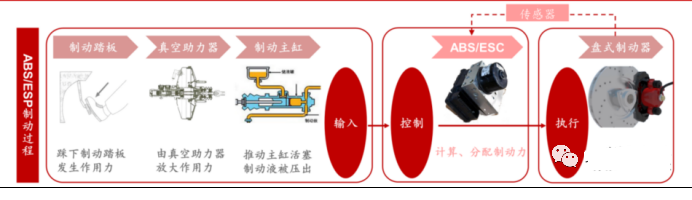
在液压制动中,踏板+真空助力器+主缸+制动器等已经是一套可以完成基本制动功能的系统了。但这个制动功能过于原始,而不具有智能功能。因此,在汽车工业发展的这么多年里,陆续出现了一些辅助功能,用于提高制动的安全性。根据对汽车安全性研究显示,在道路交通事故中,大约10%的事故是由于车辆在制动瞬间偏离预定轨道或甩尾造成的。为了减少这些问题,如今主流的行车制动系统融入了ESC系统。ESC全称是Electrical
Stability Controller,译为车身电子稳定控制系统。这些系统显然已经成为了制动系统必不可少的一部分,所以我们也有必要了解一下。前两天刷到懂车帝在漠河对各家厂商的车进行麋鹿测试,其实体现的就是车的ESC功能。
需要说明的是,虽然上图写的是ABS/ESC,但其实ESC是一些列功能的统称,其功能包括ABS。可能是有些只有最基础的ABS功能,而没有全套的ESC功能,因此上图才那么表示。本节将介绍ESC中主要的三种功能。
3.1 ABS
ABS是制动防抱死系统,那为什么要防止车轮抱死呢?汽车在制动时,如果前轮抱死,汽车基本上沿直线向前行驶,汽车处于稳定状态,但汽车失去转向控制能力,这样驾驶员制动过程中躲避障碍物、行人以及在弯道上所应采取的必要的转向操纵控制等就无法实现。
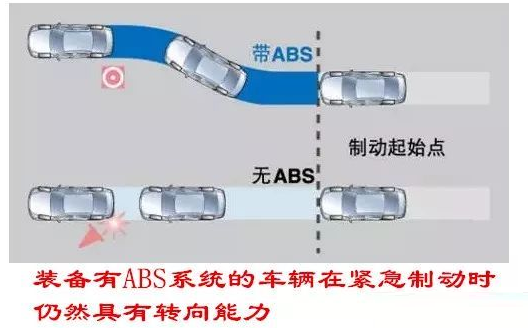
如果后轮抱死,汽车的制动稳定性变差,在很小的侧向干扰力下,汽车就会发生甩尾,甚至调头等危险现象。尤其是在某些恶劣路况下,诸如路面湿滑或有冰雪,车轮抱死将难以保证汽车的行车安全。另外,由于制动时车轮抱死,从而导致局部急剧摩擦,将会大大降低轮胎的使用寿命。
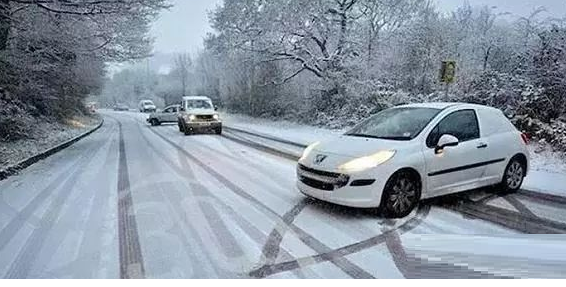
刹车就是要尽快停下来,但轮子又不能完全抱死,那制动时的最佳状态是什么?是边滑边滚,且滑动与滚动的占比在20%左右的时候,车轮与地面的附着力是最大的。为了达到这个滑移率,ABS系统会使车轮处于每秒100-200次抱死-放开这样的循环工作状态。
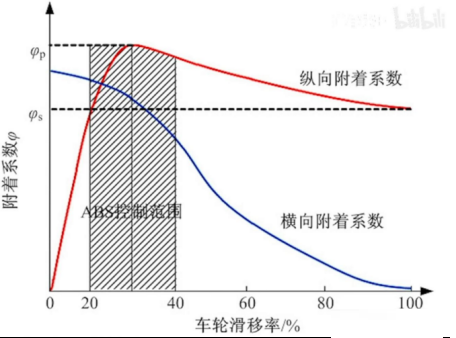
整个工作过程是四个轮速传感器实时监控四个车轮轮速并提供给液压控制单元ECU, 用以估算当前车速和各个车轮的滑移率。液压控制单元基于轮速信息判断当前车速和车轮滑移率,计算对轮缸的目标压力,并通过对液压马达和电磁阀的控制实现轮缸压力控制。
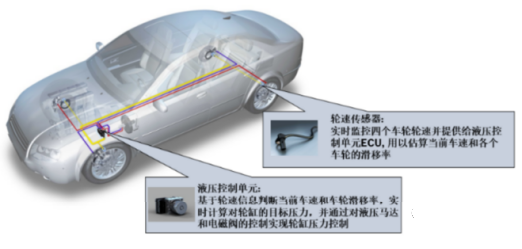
3.2 TCS
ABS激活的前提是驾驶员踩制动引起车轮有抱死倾向,因此ABS在非制动工况下的稳定性控制就束手无策了。然而,生活中同样存在非制动失稳的工况,比如:
工况1:在冰面加速起步的时候无论油门踩多深都无法起步
工况2:在分离路面(一边轮胎在附着系数低的路面而另一边轮胎在附着系数高的路面)加速起步的时候无论油门踩多深都无法起步。
为了解决这种非制动失稳,就需要用到牵引力控制系统,Traction Control System,TCS。
对于工况1,其原因在于驱动力过大使得驱动轮打滑过量导致无法合理利用路面附着力。和制动相同,当轮胎端作用驱动力时,在轮胎与地面之间都会发生相对运动,车轮中滑动成分所占的比例称为滑转率(制动对应的通常称为“滑移率”),也用S表示。从下图可知,当滑转率控制在一定范围内时才能保证车轮与路面有良好的纵向附着系数和侧向附着系数,从而为车辆提供最佳驱动力,这和ABS其实有点像,只不过ABS是要把制动力控制在一个范围内,TCS是要把驱动力控制在一定范围内。
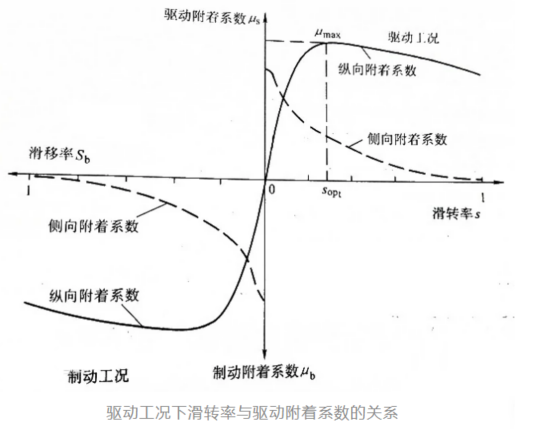
对于工况2,由于两边车轮的驱动力是一样的。这就导致了两边车轮的滑移率不一致,比如当右边的车轮的驱动力能够使车轮转动,那么这个驱动力会使得左边车轮滑移率太高,即打滑。为了使左边的滑移率在某个范围内,就需要对左边车轮增加制动力,以保证两边的车轮的滑移率都控制在特定范围。所以,TCS系统不仅需要控制驱动力,也要控制制动力。
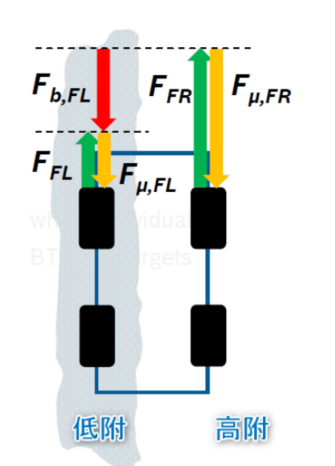
TCS控制系统是在ABS的基础上发展而来,后者在过度制动时起作用,前者在过度驱动时起作用。由于TCS不仅可以调整制动压力,也可以调节发动机或者驱动电机的驱动力,因此TCS的组成部分相对ABS要更多,除了执行机构增加了驱动力控制单元(发动机ECU或电机ECU)外,还增加了方向盘转角传感器和惯性传感器。
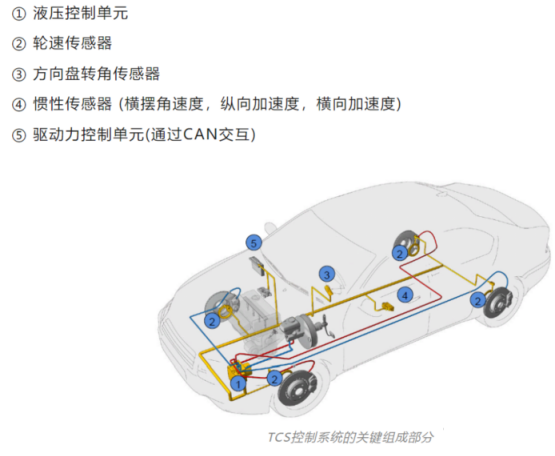
TCS通过发动机或者驱动电机的输出扭矩和轮缸压力的协调控制,调节驱动轮的滑转率,从而改善轮胎和路面间的附着特性,提高车辆的动力性和稳定性。目前主流的TCS系统控制架构如下图所示。TCS
控制器主要包括三个部分:道路状况识别、驱动扭矩控制、压力控制。
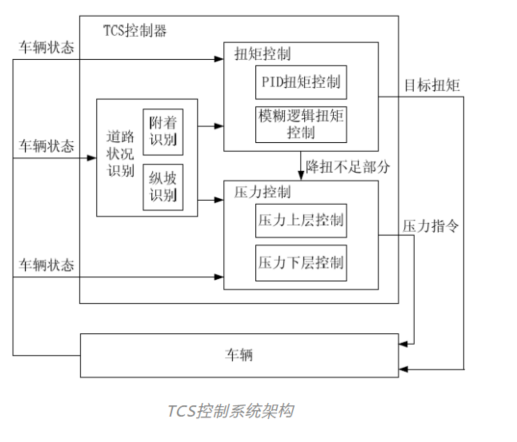
其中,道路状况识别模块主要包括附着识别和纵坡识别,根据车辆状态参量,识别出附着和纵坡,给扭矩控制和压力控制提供数据支持。驱动扭矩控制模块包括PID的扭矩控制和模糊逻辑扭矩控制两部分,其输入参量为车辆状态以及道路状况识别模块识别的路面附着和坡度,其输出参量为目标扭矩以及降扭不足部分。压力控制模块的输入为车辆状态、道路状况、以及扭矩控制模块输出的降扭不足部分。压力控制模块包括上层压力控制和底层压力控制,上层压力控制给出目标压力,底层压力控制负责目标压力的实现。
3.3 VDC
ABS只在制动时起作用,TCS只在驱动时起作用。但二者都只能解决车辆纵向稳定性问题,无法解决车辆在各种情况下的转向时引起的侧向稳定性问题。
侧向不稳定主要有两种场景,即转向不足和转向过度。就是说,当方向盘打了一定的角度,而车身摆动的角度比预期的多或者少。当出现转向不足时,横摆角速度太小,导致车辆前轴滑向弯道外侧;当出现转向过度时,横摆角速度太大,导致车辆后轴滑向弯道外侧而引起甩尾。为了这一问题,需要引入稳定性控制功能VDC(Vehicle
Dynamic Control)
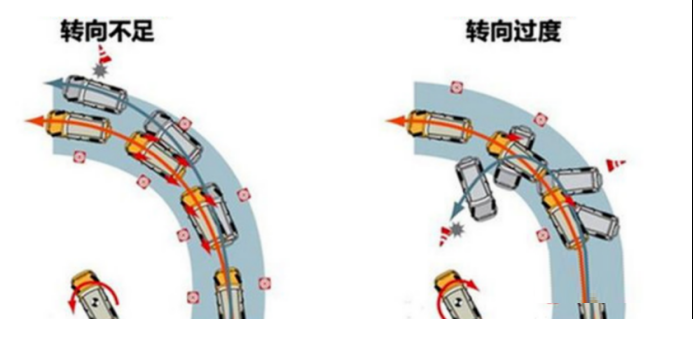
实现VDC功能的关键部件如下图所示。
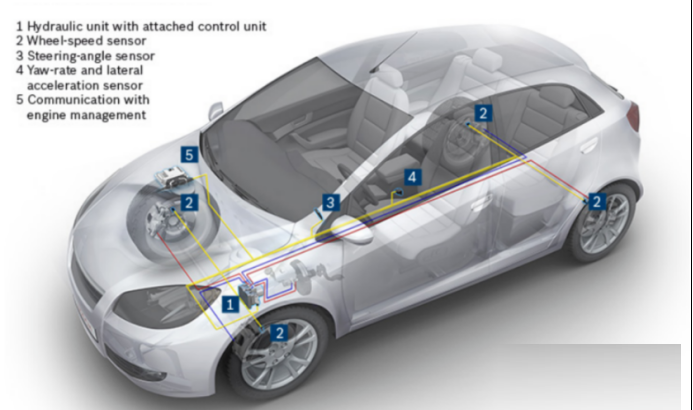
关键组成部分包括
① 液压控制单元
② 轮速传感器
③ 方向盘转角传感器
④ 惯性传感器(横摆角速度,纵向加速度,横向加速度)
⑤ 驱动力控制单元(通过CAN交互)
其中,轮速传感器通过滤波和计数技术实时计算四个车轮的轮速信息,方向盘转角传感器实时监控方向盘角度,惯性传感器实时监控车辆横轴和纵轴的动态行为,这些表征车辆状态的信息输入给ECU,通过VDC核心算法决定对轮缸液压力以及发动机或者驱动电机的驱动力,以实现对车身姿态的实时调节,保证车辆始终表现出较好的稳定性可操控性。
VDC的功能架构如下图所示。VDC实现技术主要包括控制器、控制算法、执行机构 以及系统匹配标定等,其中控制算法是VDC技术的核心
。控制算法的实现需要解决三个方面的问题:驾驶员驾驶意图的识别、汽车动力学状态的观测以及针对不同动力学状态的控制方法。
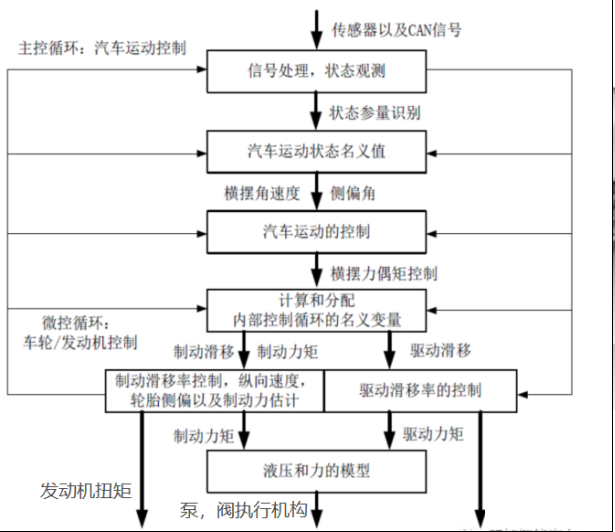
当出现转向不足时,横摆角速度太小,导致车辆前轴滑向弯道外侧,此时VDC通过对弯道内侧的车轮施加制动力而使车辆产生一个反向的横摆角速度,从而将车辆稳定在预期车道内。
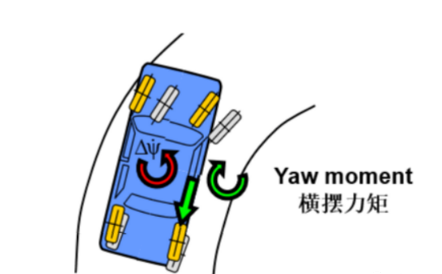
当出现转向过度时,横摆角速度太大,导致车辆后轴滑向弯道外侧而引起甩尾,此时VDC通过对弯道外侧的车轮施加制动力而使车辆产生一个反向的横摆角速度,从而将车辆稳定在预期车道内。
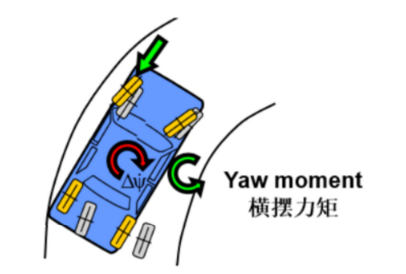
B站上有讲ESP工作原理的视频,但是看内容更像是讲VDC的,可以看下面这个链接。参考视频链接
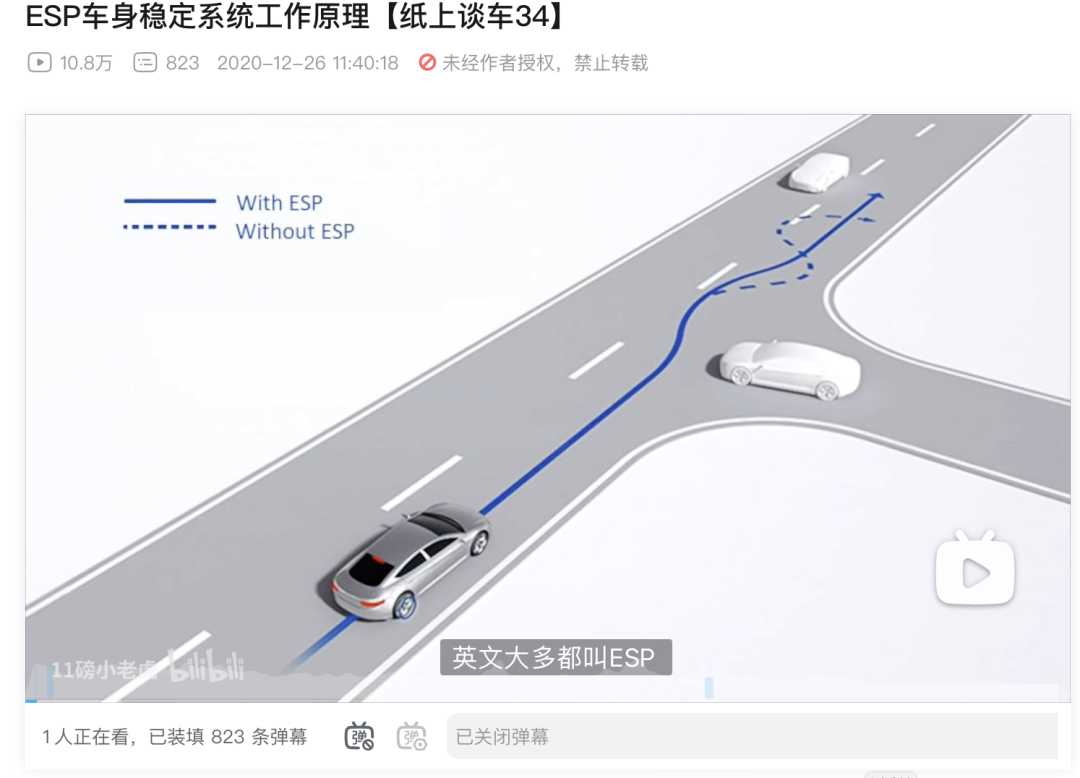
博世公司于1992年在ABS/TCS的基础上开发了旨在解决车辆侧向稳定性问题的第一代稳定性控制系统VDC,并将同时集成了ABS/TCS和VDC功能的产品命名为ESP(Electronic
Stability Program)。
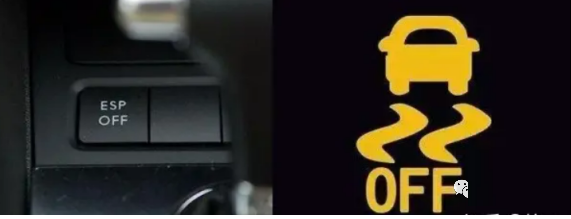
后面其他厂家也陆续推出类似产品但是无法继续使用ESP这个简称,因此命名五花八门,不过都统称为电子稳定性控制系统ESC(Electric
Stability Controller),大家在看到不同缩写的车辆稳定系统时不要疑惑。研究表明,VDC功能可以减少80%由侧滑引起的交通事故,并将严重车祸的数量减少50%。因此继承了VDC功能的ESC被多家世界著名汽车厂商和研究机构称之为“能拯救生命的ESC”。下图是博世的第9代ESC模块。
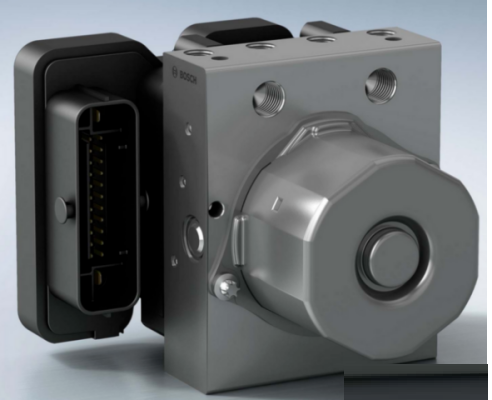
2009年欧盟强制要求从2011年11月1日起,所有在欧盟地区销售的新车都要强制装备车辆稳定控制系统,所以现在的欧洲新车都将会标配ESC。在中国虽然没有强制法规要求,但是发展到今天,10万以上的车型几乎都搭载了ESC。正是ESC在保障驾驶安全方面的不可替代的作用让它能够在市场得到如此广泛的认可和应用。从这个角度看,说集成了VDC功能的ESP产品为划时代的产品毫不为过。
ABS、TCS和VDC只是ESC中的主要功能,有的厂家还会附送其他的一些功能,有兴趣的朋友可以看如下文章扩展一下。看完ESC后,我们继续看制动方式的演进。
电子真空泵行车制动
在看真空助力器原理的时候,大家应该有注意到。助力器的真空是由于发动机工作时抽取助力器内空气造成的。到了新能源车时代,由于车内没有了发动机,这就使得制动系统要升级改造。
首先出现的是电子真空泵方案,Electronic Vacuum Pump。这套系统没有放弃真空助力,只不过采用电动真空泵EVP(Electronic
Vacuum Pump)作为真空源,其他的原封不动。这对于整车的刹车系统改动非常小,因而开发成本很低。在一些油改电项目上,可以得到应用。
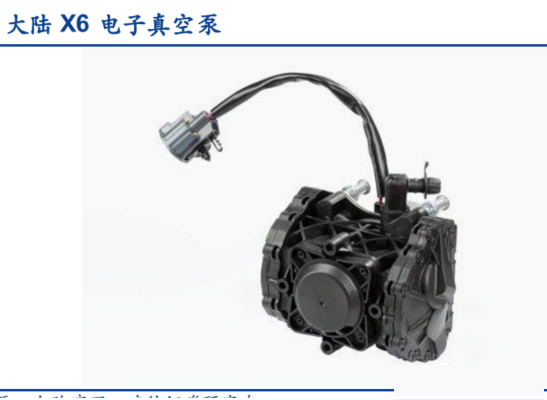
但其缺陷也很明显,首先其根本原理与传统的真空泵刹车一样,刹车踏板与制动缸之间存在机械连接,最终的制动力还是由“人脚力
+ 真空泵辅助力”合并产生,这仍然是机械传动,而非线控系统,并不能满足ADAS/AD的需求。
其次,在电动、混动车上采用该系统,能量回收的效率较低。这是因为机械连接的特性决定了,当人脚踩下踏板时,会直接引发真空泵工作,将很大的刹车力道传导到车轮上;这时候,“通过电磁感应进行的能量回收”在制动过程中的占比就会相当有限。对这段话有必要解释下。
传统燃油车依靠制动器的摩擦力消耗车辆动能进行制动,刹车产生大量的能量耗散,但燃油车对油耗的敏感程度不高。新能源汽车为了提高续航里程,大多配有制动能量回收系统,电车的车轮由电机带动,当想制动时,就把油门松掉,电机断电。车轮电机完全是由于惯性在转动,车轮转动带动电机转动,电机线圈切割磁感线,用于发电给车身电池充电,这一过程其实是将动能又变回了电能,这里不展开发电机的原理。
动能回收的方式主要有三种。
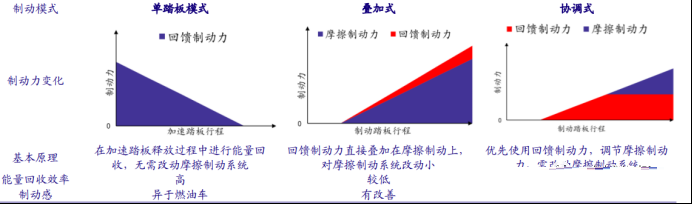
(1)单踏板模式
在单踏板模式下,相当于指依靠电机回馈制动,就是指电机的动能迅速消耗转变为电能,所以只要松开油门电机就会产生明显的反向制动力,该模式能量回收效率最高,但制动体验异于传统燃油车,驾驶员需要一定时间适应。特斯拉的单踏板模式就出了很多问题,人们养成的习惯是在紧急情况下猛踩刹车,这几乎成了很多人的本能,而单踏板模式的急刹是需要驾驶员抬起单踏板。这就造成很多人在紧急情况下猛踩踏板,反而加速了。对此,我个人觉得马斯克还是过于高傲了些,这是在教育用户,而且是以某些用户生命财产安全为代价教育用户,成本太高了些。
(2)叠加式
叠加式是指踩下制动踏板,制动器工作的同时,电机动能也在发电开始产生反向制动力,该模式下能量回收效率低。单踏板模式是靠发电机工作时产生的反向扭矩制动的,而叠加式则是主要靠制动器制动,在此过程中,部分能量变成热能耗散了,所以回收的电能比较低。
(3)协调式
协调式优先使用电机制动力,在电机制动力达到峰值后引入摩擦制动力,在维持原有驾驶体验的同时大幅提升了能量回收效率。如何优先使用电机制动力?对于传统液压式制动或者电真空泵方案,只要驾驶员踩下刹车,不管你愿不愿意,主缸内的制动液就会被传送到制动器内,产生制动力,然后刹车片被摩擦,动能转变为了热能。为了优先使用电机去制动回收电能,我们需要使得刹车踏板和制动器解耦。当驾驶员踩下刹车后,仅仅产生一个刹车信号,我们可以根据这个刹车信号去判断此时驾驶员想要获得多少制动力,然后我们就可以依次来分配制动力的生成方式。
5 EHB行车制动
电子真空泵(EVP)的优点在于改造成本低,但因其使用寿命无法和刹车系统匹配、噪音较大、受环境影响大(高原地区无法获得足够的真空助力)等缺点,且不满足自动驾驶人机解耦的要求,所以其无法成为制动系统长期的解决方案。
真空泵本质上是助力的,是为了推动主缸的活塞,将制动液压送到制动器内。那除了真空泵意外,其实电机也可以提供动力。于是就产生了Electronic
Hydraulic Brake方案,简称为EHB。
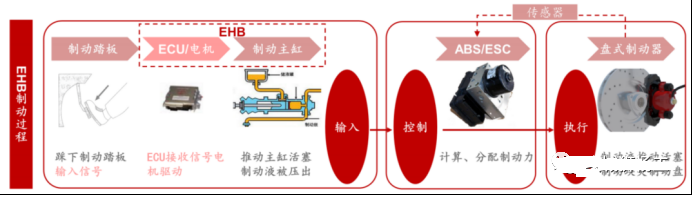
该系统彻底放弃了真空助力的方式,而直接采用前面提到的电机+减速器的电动伺服驱动主缸(如Bosch的iBooster),或采用电机+泵的电液伺服提供液压力驱动主缸(如大陆的MKCx),这与近年来电机技术的发展是脱不开关系的。
显然,电动机也更为容易实现十分精确的制动力输出,这对于ADAS/ AD系统是十分重要的。更为重要的是,对电机的控制是线控系统,而非机械传动,可以通过电信号驱动电机动作。
再然后,原来制动系统的主缸、液压管路直到轮缸的系统维持不变,制动液仍然是动力传递的媒介。那么,这种系统就叫做电子液压制动系统,即EHB。总的来说,EHB只是将真空泵换成了电机。我们前面说了ESC已经是制动系统中不可能缺少的模块了。根据助力模块与ESC的组合方式,市面上EHB产品分为两类,即Two-box方案和One-box方案。博世的解决方案市占率很高,因此以博世的产品来介绍EHB方案。
5.1 TWO-BOX方案
Two-box方案如下。需要说明的是iBooster是博世的产品名称,各家的产品名称不一样,但相同原理的都可以叫做eBooster,就是电子助推器的意思。在Two-box方案中,eBooster和ESC模块各自独立。eBooster实现基础的制动助力功能,ESC则实现稳定性控制功能,主要就是前面提到的ABS、TCS和VDC。
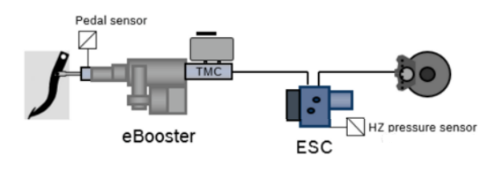
B站上有介绍Two-box方案的视频,有兴趣可以看一下。参考视频链接
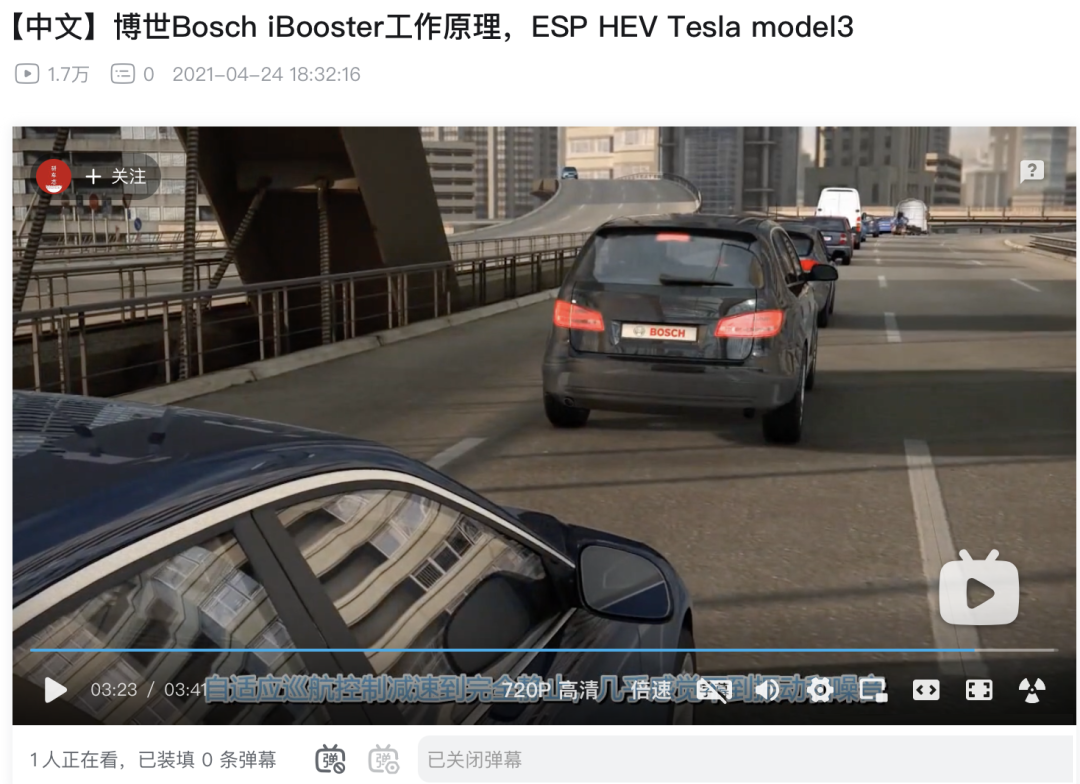
这套方案的原理如下。
(1)eBooster和ESC共用一套制动油壶、制动主缸和制动管路。
(2)eBooster内的助力电机产生驱动力推动主缸活塞运动,使油壶中的制动液流入主缸管路并进入ESC进液阀,经ESC中的调压阀和进液阀流入4个轮缸,从而建立起制动力。
(3)当eBooster不工作时,ESC也可以独立控制制动液从主缸流入轮缸,从而建立制动力。
(4)eBooster建压的动态响应速度比ESC主动建压更快,且NVH(NVH指的是噪音、振动和声音粗糙程度)表现更好,因此eBooster是制动控制系统中的主执行机构。
(5)eBooster与ESC之间有通信接口,且与整车的其他ECU也有通信接口,如下图所示。
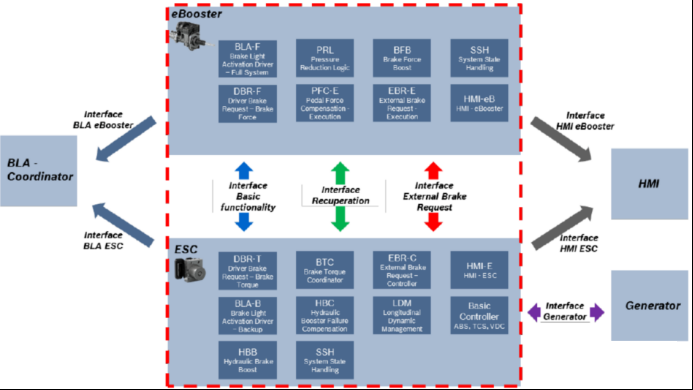
先看eBooster部分,下图是博世第二代eBooster产品。其最基础的功能是为驾驶员制动提供助力。其原理为利用传感器感知驾驶者踩下制动踏板的力度和速度,并将信号处理之后传给电控单元,电控单元控制助力电机产生对应的扭距,在机电放大机构的驱动下,推动制动泵工作,从而实现电控制动,响应速度更快并且能够精准的控制压力。
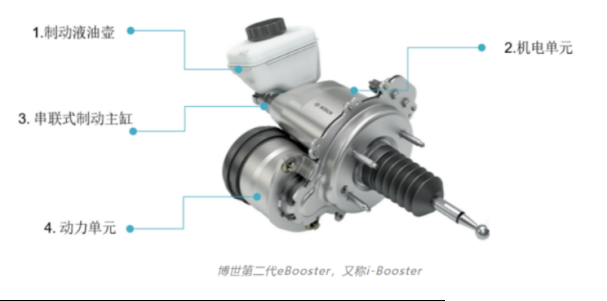
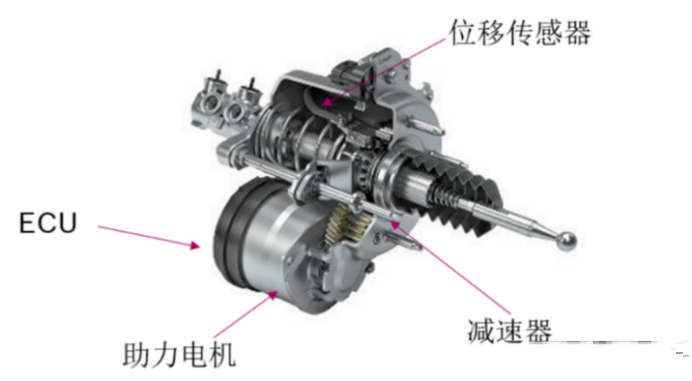
需要说明的是,eBooster属于非解耦踏板系统,即和之前的方案一样,刹车踏板与主缸有直接的机械连接。这样在制动过程中,在制动过程中eBooster能够反馈最真实和自然的踏板感,驾驶员能直观的感受到制动系统的变化。为满足驾驶感受的多样性和舒适性,eBooster还可以通过软件调节踏板感,轻松完成舒适和运动驾驶风格的随意切换。
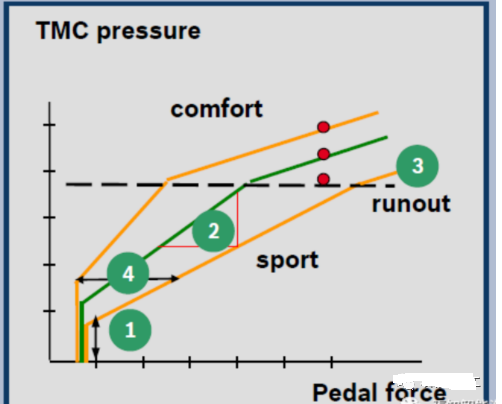
前面说过了,如果要实现协调式的动力回收,则需要踏板解耦,即刹车踏板踩下去,不能直接输出制动力,而要交给ECU去动态分配。那是否Two-Box就无法实现协调式动能回收呢?是可以的,但需要有ESC配合,下面来看ESC。下图是博世第9代ESC系统,主要提供ABS\TCS和VDC功能,除此以外还提供自动驻坡、上坡辅助等功能,这些我们不展开。
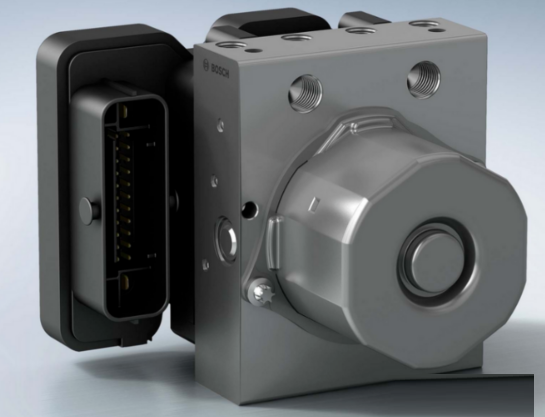
ESC系统本身有个很重要的功能,就是制动力分配。制动力分配主要有两个目的,一个是为了保证车辆不会失稳,比如当驾驶员猛踩刹车引起车轮抱死时,ESC可以通过调节主缸到制动器轮缸的液压大小来调节制动力,以实现防抱死的功能。第二个目的是,进行制动力分配以实现制动能量回收,也就是说ESC可以决定驾驶员所需的制动力哪些由液压提供,哪些由电机制动力提供。
当驾驶员踩下刹车踏板,安装在eBooster推杆处的踏板行程传感器 (Pedal Travel Sensor)
监测驾驶员踩下踏板的深度,从而反馈给eBooster的DBR-F(Driver Brake Request-Brake
Force)模块进行驾驶员意图判断。

确定驾驶员制动意图后,eBooster并不进行直接助力,而是将驾驶员制动意图通过网络通讯反馈给ESC,由ESC来进行液压制动力和驱动电机制动力分配。为了实现动力分配,必须要解除主缸制动液和轮缸制动液的直接关联。ESC会配有一个大容量的蓄能器,当驾驶员踩下刹车,主缸的制动液不会全部流向制动器轮缸,有一部分会流入ESC的蓄能器。具体多少流入制动器轮缸,这就由ESC来决定了,这样就可以实现制动过程中电机制动力与液压制动力的动态协调控制。
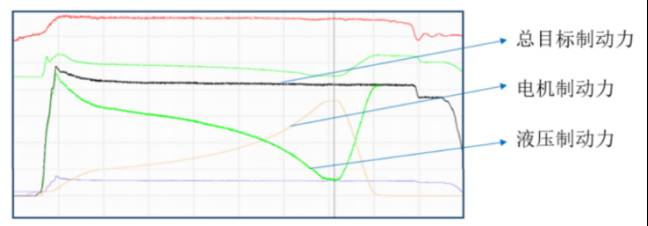
在这个过程中,由于每次直接由液压产生的制动力不一样,那有可能会有脚感不一样的情况,比如同样是踩下去一半的行程,但前后两次脚的反馈不一样。eBooster需要有个PFC(Pedal
Force Compensation)模块去保证每次的脚感一致。eBooster的弹簧力是一定的,只是不同液压制动力分配下,Fhydraulic会变化。只要根据Fhydraulic的变化,调节电机助力大小Fboost的大小,就能保证Fpedal的大小。Fpedal即驾驶员感受到的力。
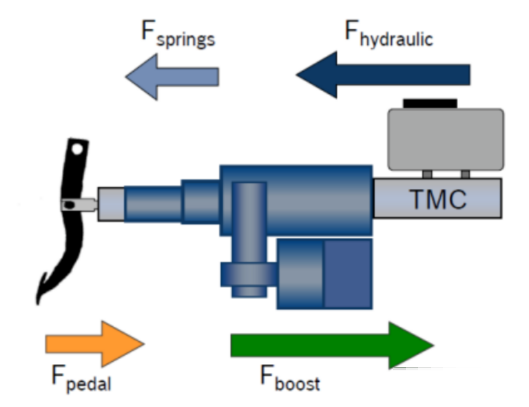
在自动驾驶应用中,不会有驾驶员脚踩刹车的动作,自驾控制器的指令会通过通信网络传递给ESC,由ESC控制整个制动系统,控制过程与上述大致相似。ESC可以自己建压(从主缸抽取制动液输送到制动器轮缸),但通常不会直接建压,而是将这些制动请求处理后转发给eBooster,由eBooster实现建压,以便充分利用eBooster建压的动态响应速度比ESC主动建压更快,且NVH表现更好的优势。
Two-Box是目前市场上支持自动驾驶的黄金组合,因为其天然满足了制动的冗余需求,并广泛运用于主流智能驾驶车型上,如Tesla全系、蔚来ES8、小鹏P7、理想ONE、长安UN-T、长城摩卡以及极氪001等。
基于eBooster和ESC系统组合开发的支持自动驾驶的冗余制动系统,ESC和eBooster分别连接一套相互独立的供电系统,且冗余上层控制单元分别控制ESC和eBooster。
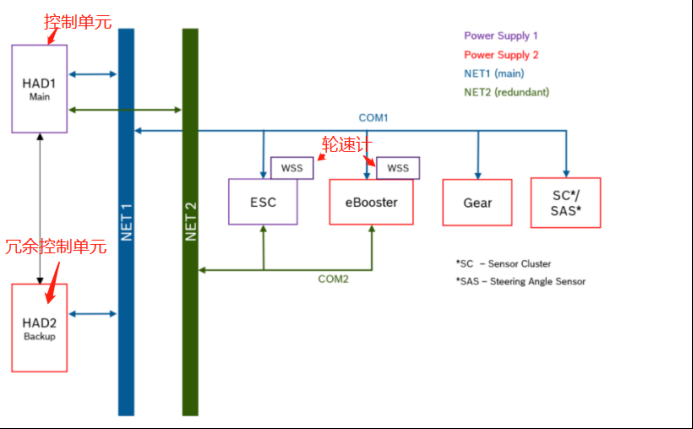
根据法规要求,对于舒适性制动系统,需要满足在驾驶员踩出500N的制动力时系统能够提供不小于6.43m/s²的减速度。正常情况下eBooster可以实现这一要求,而当eBooster出现故障无法继续提供助力时,ESC中的HBC(Hydraulic
Brake Failure Compensation)功能被激活。当HBC功能激活后,当驾驶员踩下制动踏板时,主缸压力发生变化,HBC功能根据主缸压力变化识别驾驶员制动意图,并控制建压泵工作主动建立轮缸压力,从而实现驾驶员助力。即使eBooster和ESC两套都故障了,由于EHB是非踏板解耦的,还可以依靠纯液压(无电助力)去制动。
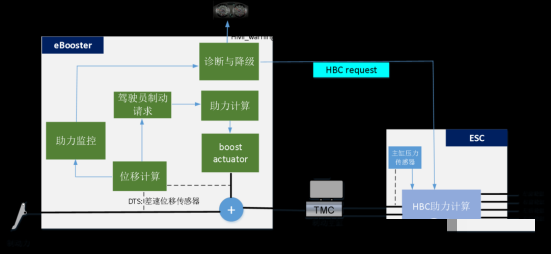
5.2 One-BOX方案
Two-box方案中,我们看到了助力系统没有和踏板完全解耦,当智能驾驶系统请求制动控制时,在驾驶员没有干预的情况下,制动踏板会根据减速度大小动态升降,因此eBooster还需要额外考虑安全设计,以确保踏板动作幅度不会夹到驾驶员的脚而引起人员伤害。这种机械表现在美国和中国市场不大受OEM欢迎。
另一方面,目前自动驾驶系统还未普及,L2及以下的智能驾驶系统对制动系统没有冗余需求,对线控制动系统的需求主要是高动态响应特性以及制动回收功能,在这种情况下,Two-box方案的体积和成本都没有优势。
在这样的背景下,集成基础制动功能和稳定性功能于一身并实现与踏板完全解耦的One-box方案开始受到更多主机厂的青睐。One-box就是将eBooster和ESC集成在一起,可以省掉一个ECU和一些机械液压结构。
One-box方案中驾驶员的踏板力不作用于主缸,踏板感通过模拟器实现,而制动力由伺服电机实现,因此踏板感调节的自由度更大。而且在智能驾驶系统控制的过程中,One-box在提供制动力的同时不引起制动踏板的动作,实现了真正的解耦。
国内外不同厂家的One-box线控制动系统的工作原理大同小异,下面以当前市场上的主流产品博世IPB(Integrated
Power Brake)为例,对One-box线控制动系统的工作原理展开说明。
IPB系统基础制动功能主要由两个部分实现:
(1)驾驶员接口模块:踏板-主缸-踏板模拟器
(2)主动建压模块:伺服电机-液压管路-电磁阀
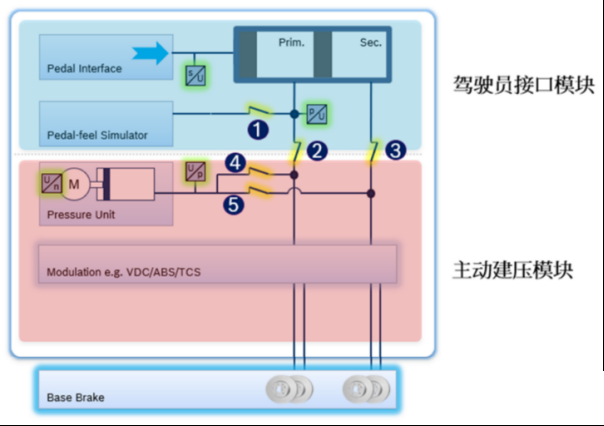
正常情况下,当驾驶员踩下制动踏板,阀2和阀3断开,切断驾驶员接口模块和主动解压模块之间的液压回路;同时,驾驶员接口模块的阀1闭合,驾驶员踩踏板后制动液进入主缸和踏板模拟器并建立压力,该压力的主要目的是给驾驶员反馈踏板感,此时踏板力-踏板行程曲线由主缸和踏板模拟器的特性决定,不同的厂家可以根据不同的喜好个性化定制踏板模拟器特性。
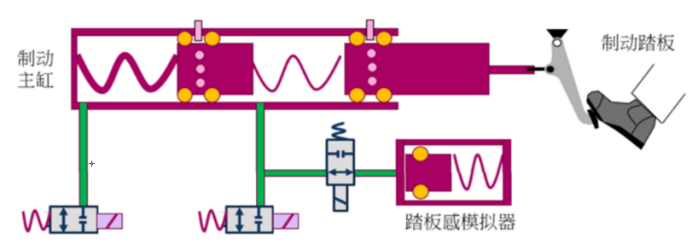
而在主动建压模块中,阀4和阀5断开,IPB ECU通过识别踏板位移信号后,伺服电机根据标定好的踏板位移-系统压力曲线建压,推动推杆将腔内的压力推到轮缸,产生车辆减速度。
如果在驾驶员制动的过程中需要稳定性系统干预,ABS/TCS/VDC通过对各轮轮缸压力或驱动力进行动态调节以实现车辆的稳定性。
而当IPB助力功能失效后,此时IPB进入backup模式,阀2和阀3闭合,阀1、阀4和阀5断开,驾驶员踩踏板建立的压力直接进入轮缸并产生车辆减速度。根据法规ECE
R13-H要求,当驾驶员输入500Nm的踏板力时,IPB的机械制动应产生不小于2.44m/s²的制动减速度。
Two-box方案中,动能回收过程中的制动力分配主要是由ESC的大容量蓄能器实现的。在大容量蓄能器的加持下,当驾驶员踩下制动踏板时,
eBooster控制主缸液压进入轮缸产生制动力,于此同时驱动电机制动力随着制动踏板深度增加缓慢上升,该过程中来自主缸的制动液不会直接流入轮缸,而是将一部分暂时存储在蓄能器中,在蓄能器中的制动液不会产生制动力,由此实现制动过程中电机制动力与液压制动力的动态协调控制。因此,蓄能器的容量决定了“eBooster+
ESC”这套组合的制动能量回收的上限,比如博世的产品组合能提供的最大制动回收减速度为0.3g。
而One-box方案天然地解除了主缸制动液和轮缸制动液的“直接关联”,且没有蓄能器的容量限制。因此,One-box方案制动回收的能力相比Two-box方案组合更强,通常为0.3g~0.5g。
但是需要指出,One-box也存在劣势。虽然在辅助驾驶系统中相比Two-box方案有较大的成本和重量优势,但是对高阶的自动驾驶系统而言,Two-box方案能够满足对线控制动系统冗余的需求,当主制动系统发生单一故障时,备份制动系统需要保证车辆仍然能够进入安全状态(如靠边停车),但是One-box方案显然无法独立完成这一任务,因此One-box需要额外配合一个独立的制动单元RBU(Redundant
Brake Unit)组成能够支持制动冗余的Two-box方案,此时成本和重量优势则不明显了。
可能有人会说,机械制动不就是冗余吗?L3及L3以上的自动驾驶,必须要有电子冗余,即系统的制动冗余,必须是另一套系统。自动驾驶等级划分如下,下图是形象的表示,严格的等级定义可以自行查询。先说L4/L5,解放大脑和没有驾驶员就意味着,当制动系统出故障的时候,需要有另一套无需人参与的冗余制动系统来接管。对于L3而言,可以解放双眼,当出现故障的问题,系统提示驾驶员接管,从系统提示到驾驶员接管,是有个时间的,对于制动这种关键环节,只要出现紧急情况,系统就撒手不管扔给驾驶员,这是不负责任的,法规也不允许。因此,对于L3级别的自动驾驶,也需要有无需人参与的冗余制动系统应对紧急情况。综上L3及以上级别的自动驾驶的制动系统都需要有电子冗余。机械冗余是最后的防线,必须要有,但仅仅只有机械冗余是不够的。
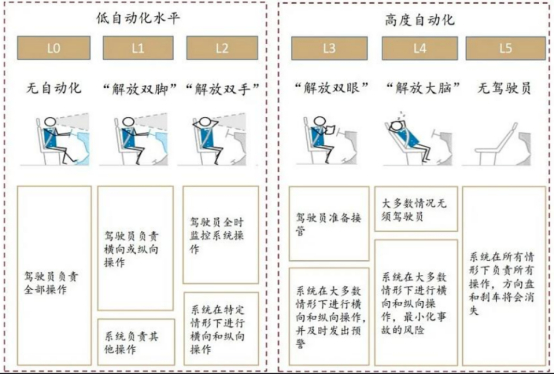
One-box的冗余方案如下。制动主缸两个腔出口的制动管路除了和One-box连通外,还连通RBU的输入端,而RBU的两路输出管路则在分别与IPB中的轮缸管路相连。当One-box系统故障时,系统进入制动备份模式,阀2和阀3闭合,阀1,阀4和阀5断开,RBU中的电机工作,将制动主缸中的液压通过阀2和阀3推入轮缸完成建压。高速自动驾驶除了要求制动系统具备基础制动功能冗余外,还要求车辆具有纵向稳定性冗余,这就需要RBU同时具备纵向稳定性控制的能力(为了实现最基本的ABS功能,需要给RBU配备冗余轮速传感器)。目前市场上的RBU方案基本都是从底盘电子稳定性系统(ESC,
Electric Stability Controller) “减配”改造而来,能够实现纵向稳定性控制。
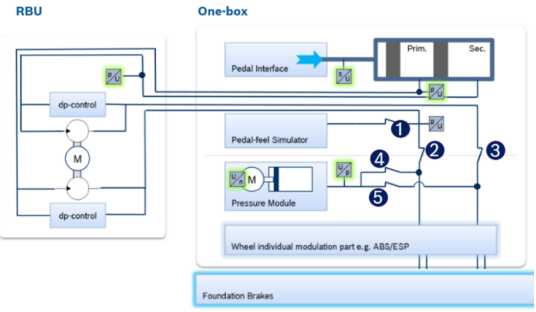
两种方案的对比总结如下。
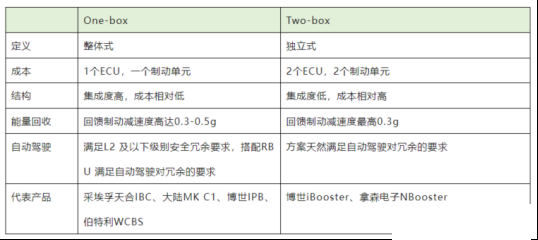
各家的EHB产品如下图所示。
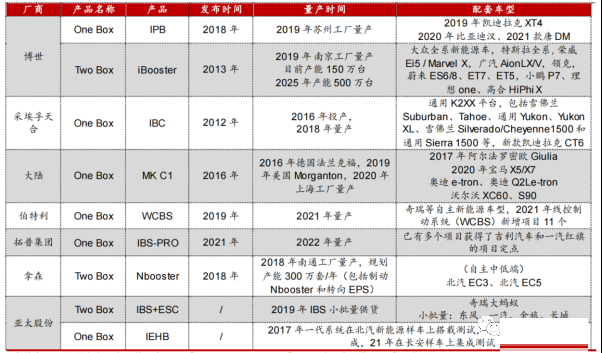
6 EMB方案
EHB方案用电机取代了真空泵,而后面的液压系统没有去掉。想一想液压系统的目的是什么?是将力通过液体传递到制动器,在制动器端,制动液进入活塞,推动刹车片,最终刹车。那是否可以将制动器端的液压系统直接换成电机,制动系统直接给电机发送指令,产生相应的制动力不就可以了。回头看下,是不是和EPB有点像。
如此一来就不需要刹车液压管路,此时,脚踏板与刹车系统之间的机械连接也彻底取消,所有信号都是通过电信号来传递,这也就是线控刹车的终极形态——电子机械制动系统EMB,Electronic
Mechanical Brake。由于EMB在每个车轮上都安装有独立的电机制动器,且不需要液压管路,因此又被称为分布式、干式制动系统。EMB系统的原理如下图所示。
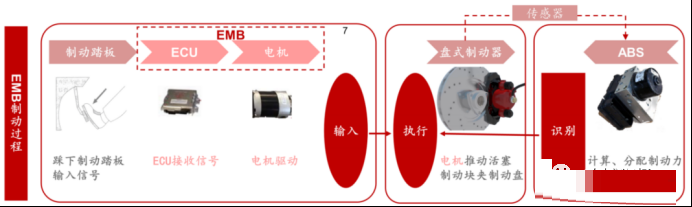
线控制动有两种方案,电子液压制动系统EHB与电子机械制动系统EMB,前者部分保留液压结构,后者直接是电子机械的结构。有必要对比一下这两种方案。
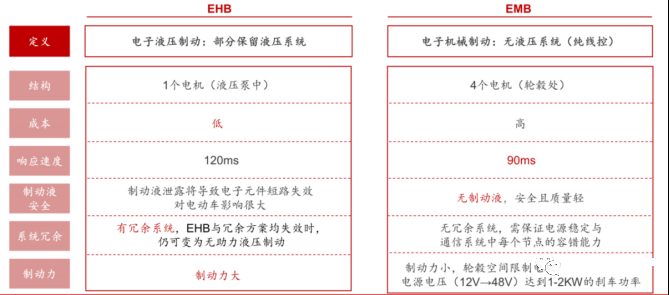
1)EHB单车成本更低:EHB只有一个液压泵的电机,将制动液传至四个车轮的卡钳处,而EMB是在四个车轮的卡钳处各装一个电机,因此EHB单车成本较
EMB 低一些;
2)EMB响应速度更快:EHB平均响应时间120ms,而EMB平均响应时间90ms,EMB在响应速度上具有优势;
3)EMB无液压装置,减少重量及漏液风险:EHB部分保留液压结构,一旦制动液泄露,将造成电子元器件短路,对电动车影响较大;而EMB无液压结构,安全且轻量;
4)EHB具备冗余备份,可靠性强:EHB目前冗余备份方案相对比较成熟(eBooster+ESC),即使电控冗余方案也失效了,也可以变为无助力的液压制动系统,驾驶员用力踩制动踏板时仍可实现制动。而EMB由于电机直接位于卡钳处,一旦出现断电、电机故障、电路短路等问题,制动系统将直接失效,安全隐患较大;
5)EHB对制动电机要求更低:从制动力大小的角度看,EMB 如果要实现与 EHB 相同水平的制动力,对电机功率要求较大,需要增加电机体积、达到1-2,000KW的功率,匹配48V高压电源,目前相关技术还不能够满足这一要求。
综合来看,EMB是在理论上的理想方案,但由于冗余备份、电机功率等关键技术没有突破,预计5-10年线控制动仍将以EHB为主。
前面说了,EMB和EPB有点像,但EMB对系统的要求显然要比EPB要高的多,不管是电机功率还是可靠性要求等。那么可以预见,当EMB成熟后,EPB也就没有存在的必要,到那时就不必再分驻车制动和行车制动了,EMB都可以搞定。
7 写在最后
以上梳理了线控制动的相关内容,线控制动是线控底盘中最关键,也是最难的部分,因此单写了一篇文章,后续将继续学习线控底盘的其他部分。
|